By Andy Guerra and Ryan Ayres
At face value, the idiom “the devil is in the details” may seem dark when describing common failure points of a building envelope. However, in the in the case of building flashing, it’s true. No matter where we are in the country, from the Carolinas to California, the most common construction defects are associated with water intrusion. To that end, the details and diligence in installation matter. So why do we continually see installation defects of these elements, and more importantly, who’s responsible?
Flashing Defects
The answers surrounding responsibility are multifaceted and typically include improper or insufficient direction from design professionals, deficient or incomplete installation of the flashing systems by the contractors, or a combination of the two. This is further complicated when considering allocation of responsibility for such defects. Upon expert investigation and evaluation, water intrusion is generally found to be attributable to insufficient, defective, or improperly executed flashing. To properly construct a building, flashing around doors, windows, and other fenestrations are required to ensure code compliance and proper performance of the building envelope. The International Building Code (IBC) states, “flashing shall be installed in such a manner so as to prevent moisture from entering the wall or redirect that moisture to the exterior.” Experience has shown that water intrusion often occurs when moisture exploits construction defects in exterior walls, roofs, windows, and doors at flashing locations, with such defects occurring at increasingly high rates.Common Causes of Flashing Failures Leading to Construction Defect Litigation
To make sense of the litany of claims and counterclaims, it’s inherent to remember that design professionals provide the concept, design, and installation details, while contractors take these concepts and bring them to life. However, when the design or the execution of the installation of flashing systems fails to prevent moisture intrusion, litigation is often likely and anyone with experience in construction defect litigation knows that once fingers start getting pointed in every single direction, no parties will be left unscathed. At this point, forensic experts are called to evaluate the cause and origin of the alleged failure. Through investigation, forensic evaluators commonly find the following to be the primary causes of flashing system defects: Construction Deficiencies: Missing and/or improper installation of flashing materials; deficient integration of flashing materials with roofing, windows, doors, etc.; and substitution of improper/unapproved flashing materials. Design Deficiencies: Insufficient details/direction within the construction documents; direction contrary to the fenestration or flashing product manufacturer’s instructions; reliance on contractor inference to properly integrate various and differing product requirements; and specification of materials that are incompatible with site conditions. Product Deficiencies: Improperly manufactured flashing materials/elements; and incompatible materials used in conjunction with each other.Flashing Failures are Here to Stay
These common defects and deficiencies should come as no surprise to a seasoned construction defect claims or litigation professional. This is attributable to various conditions including the increase and change in requirements of building codes, ever varying and changing manufacturer requirements, the trend toward design professionals attempting to transfer liability to construction professionals, and the overall decrease of the availability of skilled labor within the construction industry. Each of these attributes leave us with the reality that design, construction, and manufacturer errors will continue to happen, resulting in moisture intrusion due to improper flashing. We can only hope that as construction defect litigation continues across the country, that both design professionals, contractors, and system manufacturers alike will focus on the details and make changes within the respective fields to reduce the “devilish” consequences of such defects.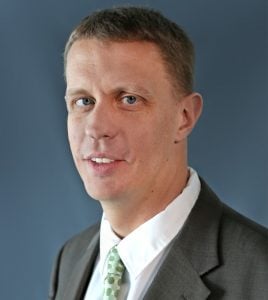
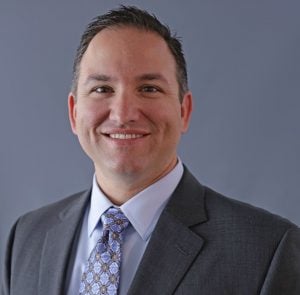